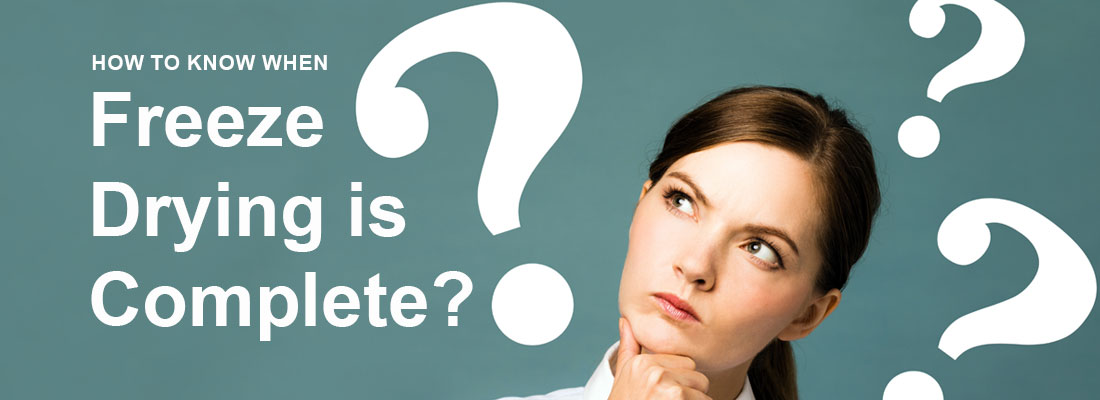
How do I know when freeze drying is complete?
Freeze drying, also known as lyophilization, stands as a pinnacle in preservation technology, with applications spanning diverse industries. The culmination of a successful freeze-drying process involves a careful selection and orchestration of techniques. A key question across all these industries is “How do I know when Freeze Drying is complete?” There are a wide range of techniques available, and these are often dependant on the industry and the sophistication of the freeze dryer being used.
1. Visual Inspection
For users of simple manifold freeze dryers, visual inspection is a primary method of determining whether your samples have completely freeze dried, but it has its limitations:
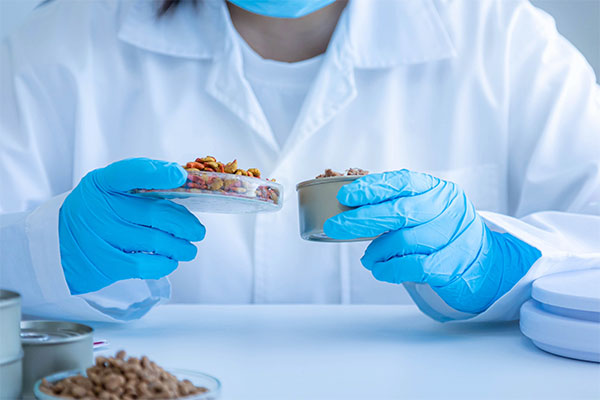
Subjectivity: Visual cues can be interpreted subjectively, leading to variations in determining the endpoint. This subjectivity may not align with the precision required in regulated processes.
Lack of Quantitative Data: Visual inspection provides qualitative insights but lacks quantitative data. It doesn’t offer information on critical parameters like moisture content, essential for ensuring product stability.
These limitations emphasize the need to complement visual inspection with more objective and quantitative techniques for a comprehensive assessment of freeze-drying completion.
2. Cycle Time Analysis
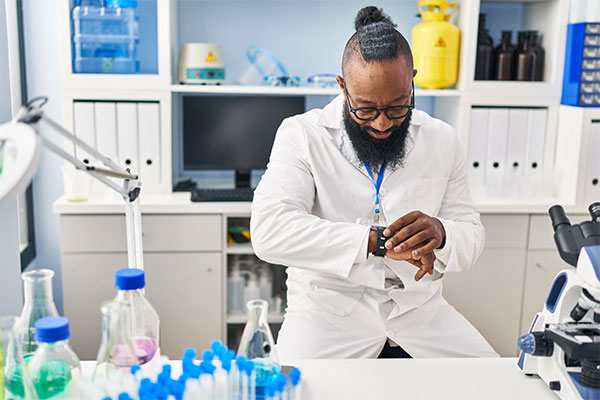
Cycle time is a reliable parameter applicable across various freeze dryer types when determining whether your samples have completely freeze dried. Pharmaceutical companies utilizing sophisticated freeze dryers often set a predetermined cycle time for the entire process, including freezing and drying phases. This method is similar to setting a timer, ensuring that the product undergoes the necessary transformations before reaching the desired state.
3. Weight Change as an Indicator
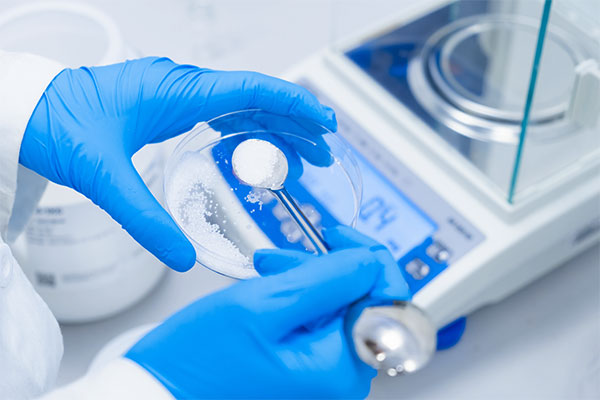
An effective approach within moisture content analysis is tracking weight change. This can occur either after the freeze-drying process or in real-time. The endpoint is marked by a consistent product weight, indicating drying completion. It’s crucial to note that real-time weight monitoring requires specialized scales placed inside the freeze dryer. However, these scales can be costly and typically monitor a single vial, limiting their widespread use.
4. Moisture Content Analysis
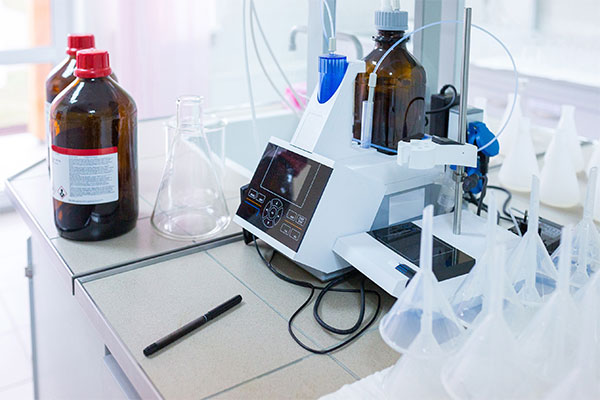
In high-tech freeze dryers, the in-depth analysis of moisture content plays a pivotal role in determining process completion. This technique involves employing analytical methods like Karl Fischer titration and moisture analysis to quantitatively assess the moisture content throughout the freeze-drying journey. Real-time moisture content readings offer a dynamic view of the drying progress, ensuring the endpoint aligns precisely with the desired moisture levels for product stability.
Weight Change as an Indicator:
A practical aspect of moisture content analysis involves monitoring weight change. This can be done either post-run or in real-time. When the weight of the product remains constant, it signals the completion of drying.
5. In-Process Monitoring
In high-tech freeze dryers, in-process monitoring stands at the forefront of precision. This technique involves real-time observation and meticulous control of critical parameters:
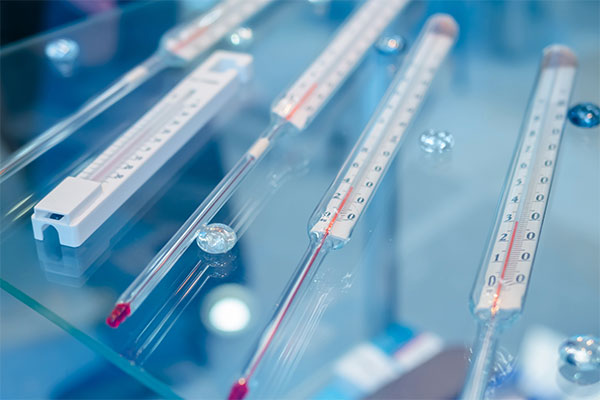
a. Temperature Monitoring: At the start of the freeze-drying process the product temperature will be colder than the shelf temperature. This is due to evaporative cooling which takes place during sublimation. As the sublimation rate slows, the product temperature will slowly increase until there is no evaporative cooling taking place and the product temperature will equal the shelf temperature.
b. Pressure Readings: Advanced pressure measurement tools like Pirani and Capacitance manometers provide an extra layer of sophistication. Pirani gauges measure a wide pressure range, offering insights into vacuum conditions, while Capacitance manometers provide accurate readings in low-pressure environments. Pirani and capacitance manometer readings are affected by water vapor. In the initial stages of primary drying, when there’s a significant amount of water vapor, the Pirani reading tends to be higher than that of capacitance manometers. As primary drying progresses and water vapor decreases, the Pirani reading gradually converges with that obtained by the capacitance manometer. This convergence point can serve as a crucial indicator, signaling the potential end of primary drying.
An alternative pressure reading method is the Pressure Rise Test. Here, the sample chamber is sealed off from the condenser using a valve. If the pressure within the sample chamber rises, it indicates ongoing sublimation.
c. Mass and Heat Flow Measurements: Monitoring mass and heat flow becomes increasingly nuanced in advanced setups. Sensors measure the rate at which water vapor leaves the product and the corresponding heat changes. This dynamic measurement provides quantitative insights into the progress of drying and allows for on-the-fly adjustments, ensuring optimal energy efficiency and product quality.
Conclusion on how to know freeze drying is complete
Determining the end of freeze drying is an art and science combined, where techniques range from the simplicity of visual inspection to the sophistication of in-process monitoring and moisture content analysis.